COMPOSTRONICA 2.0
The evolution of "Compostino"
Development of proprietary sensor boards
After the experience accumulated by the projects "Compostino“, developed in collaboration with ENEA “Casaccia”, we decided to focus on the specific needs that the electromechanical composting environment requires.
Sensors of different technologies and of high precision carefully chosen for the purpose, combined with control boards developed specifically for this use environment, provide this new monitoring system Compostronica 2.0 better reliability and perfect control of the biological process in progress.
The calibration of these sensors is carried out during their manufacture and is guaranteed for 24 months. At the end of this period of time, the accuracy of the measurements will gradually degrade and the sensors will need to be re-calibrated.
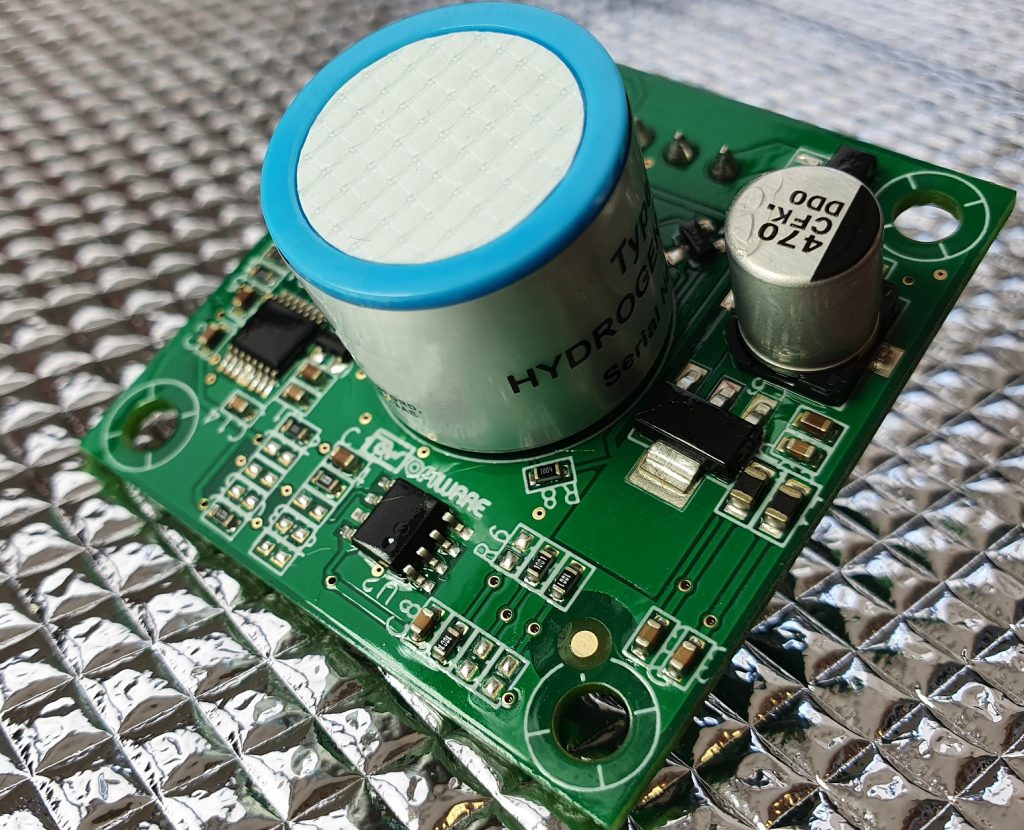
Improved manufacturing process
A small company like ours needs a solid project and a reliable supply channel to be able to meet customer requests, so we focused on improving its production process as much as possible so as to facilitate assembly and then installation on site.
Milling of aluminum and plastic with numerical control machines (CNC), 3D printing with selective laser synthesis (SLS) and extrusion (FDM) technologies make production more precise and in series.
Simple Design
The new look of the Compostronica 2.0 it is simpler and more linear than its predecessor Compostino, thanks to the use of plastic materials and internal and external components printed in Nylon with Jet Fusion technology.
The resulting product appears more refined, lighter and easier to use.
A touch display allows you to navigate in the various menus (function that can be disabled remotely), providing information regarding the measurements. The message function allows a text that can be sent remotely to appear on the screen, so as to advise the driver of any corrections to be made to improve the efficiency of the device.
An artificial intelligence that generates messages automatically and is currently under development.
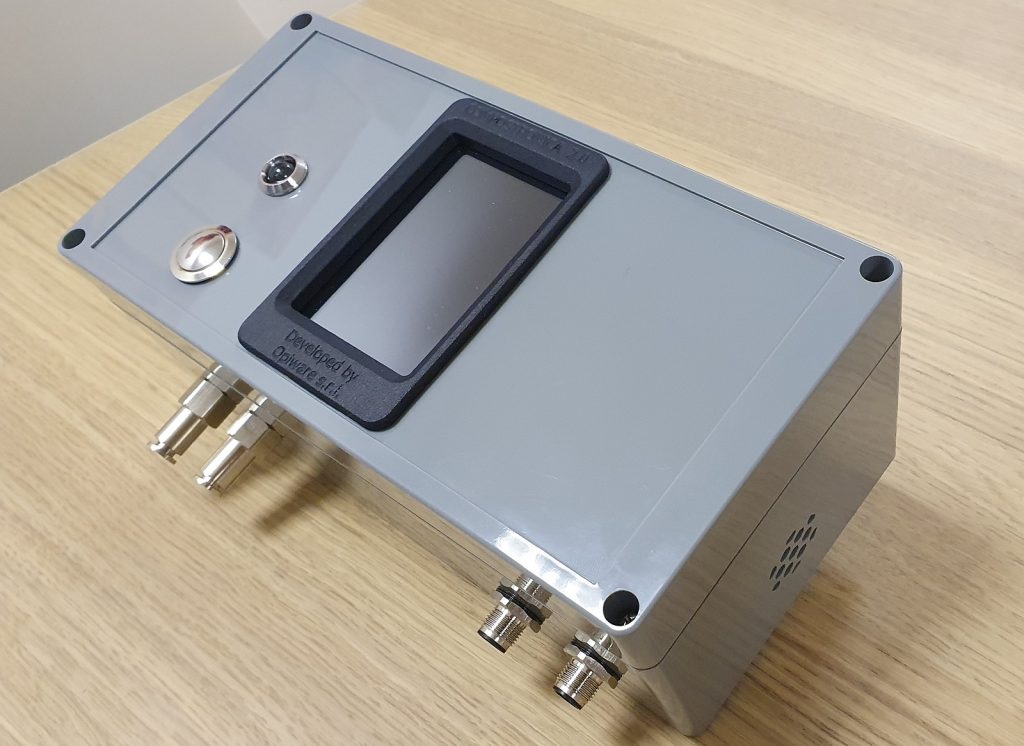
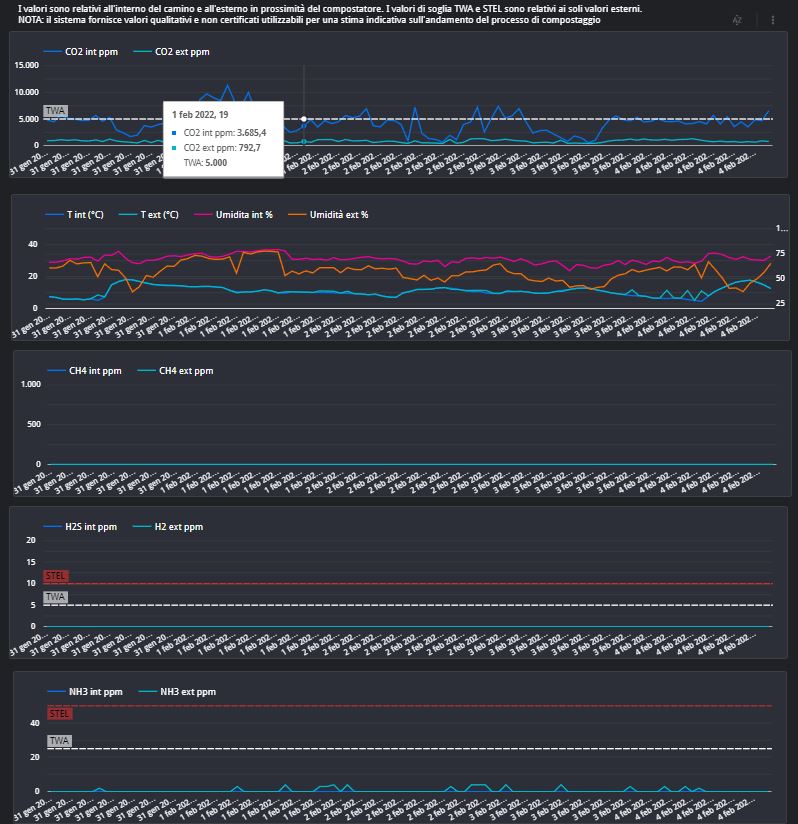
Data remotely
The strong point of the system Compostronica 2.0 is undoubtedly the possibility of graphically displaying the data recorded and sent by all the devices.
This visualization takes place through a simple link that can be opened with a normal internet browser which allows access to a page hosted by our site. These screens are customized with any logos and functions that the customer requires.
Graphs of various sizes and types make the recorded data easy to interpret and understand for anyone. A window allows you to select defined time frames so as to make navigation through the recordings even more immediate. A table showing the data not expressed in the graph can still be viewed. There is also an indication of the last connection of the system to the internet.
It is also possible to access the data in a more direct and less elaborate way, viewing the recordings without any graphics. There is also the function for downloading a file in Excel format containing the data, so as to allow the customer to process them at will with personalized graphics and to keep their electromechanical devices under control even more efficiently.
Basic features
- Wall installation via 35mm DIN rail, one of the most widespread standards for a plug and play philosophy.
- 220V alternating current power supply, with a flying connector supplied at the time of purchase.
- Quick coupling interface for 2 ø6mm external diameter pipes, 1 for the suction hood of the machine, the other for washing (not necessarily connected to a pipe).
- External dimensions 238x118x110mm.
Sensors for detecting the biological process
- Catalytic methane sensor CH4: 0-100%.
- Electrochemical ammonia sensor NH3: 0-1000ppm .
- Electrochemical Hydrogen Sulphide sensor H2S: 0-100ppm.
- Infrared carbon dioxide sensor CO2: 400-100’000ppm.
- Sensor Temperature: -25°C – +85°C.
- Sensor Relative Humidity: 0-100%
Basic functionality of pumps
There are 2 electric pumps installed: the first for the suction of the gases released by the system, the second for washing the sensor chamber so as to preserve its premature degradation. However, washing does not prevent you from carrying out a second analysis of the air coming from the surrounding environment.
This process has a threefold function: it provides a comparison picture with the data collected from the plant, monitors any gases indicating bad smells outside the hood and ensures that operators and conductors work in an inert and compliant environment.





Why measure these values?
CO2 – Carbon dioxide
This gas is the waste product of bacterial respiration and provides a very important indication regarding the aerobic process of decomposition of organic waste.
H2S – Hydrogen sulfide
With a very strong odor, it is one of the most important gases to monitor. It is a marker of anaerobic processes and is dangerous for human health even in a few ppm.
CH4 – Methane
The presence of high concentrations of this gas may indicate that the decomposition in progress is turning towards an anaerobic process and therefore interventions by the operator are necessary.
C° – Temperature
Measuring the temperature of the air discharged from the chamber is one way to ensure that the internal biological process is in good health and working in an efficient environment.
NH3 – Ammonia
This gas is an indicator of a high presence of nitrogen, and therefore a low ratio between this and carbon. In high concentrations it can also be harmful to human health.
% - Relative humidity
Relative humidity is an indication of how much vapor is contained in the air. Measuring this value is an index of the process of reducing the presence of water in the compound.
Additional Information:
The measurements are carried out at the air emission of the biofilter and in the work area where the operators are present with indication/alarm of exceeding the thresholds:
TWA (Time Weighted Average) are the concentration values averaged over a working day of eight hours per day and over 40 hours per week;
STEL (Short-Term Exposure Limit) represents the concentration values for short exposure, usually averaged over 15 minutes; this exposure cannot be repeated more than four times a day, ensuring at least an hour's interval between successive exposures;
The data acquired from Compostronica 2.0 they will be sent every hour to a server via GPRS (General Packet Radio Service, essentially the SIM-based system with which we connect to the internet) which will save them on a database. The system will return commands to change the operating parameters (e.g. revolutions per hour, suction fan speed, etc.) or direct messages to the operator (e.g. add structuring agent) based on the acquired data. The return of commands (technically retroaction or feedback), in addition to optimizing the process, gives the possibility to access the advantages offered by the "INDUSTRIA 4.0“.